Carbon Fiber Aerospace Structures: Properties and Applications
As carbon fiber composite technologies continue to evolve, their applications in the aerospace industry are rapidly expanding. At Sanse (cn-frp.net), we specialize in delivering high-performance, lightweight carbon fiber aerospace structures that meet the growing demand for strength, rigidity, fatigue resistance, and fuel efficiency in modern aviation.
1. What Are Carbon Fiber Aerospace Structures?
Carbon fiber aerospace structures refer to structural components made from continuous carbon fibers reinforced with resins such as epoxy, PEEK, or BMI. These composites are widely used in the load-bearing sections of aircraft and spacecraft.
- Wing components (spars, skins, wing boxes)
- Fuselage sections and connectors
- Vertical and horizontal stabilizer frames
- Cargo doors and landing gear covers
- Fairings, intake ducts, radomes
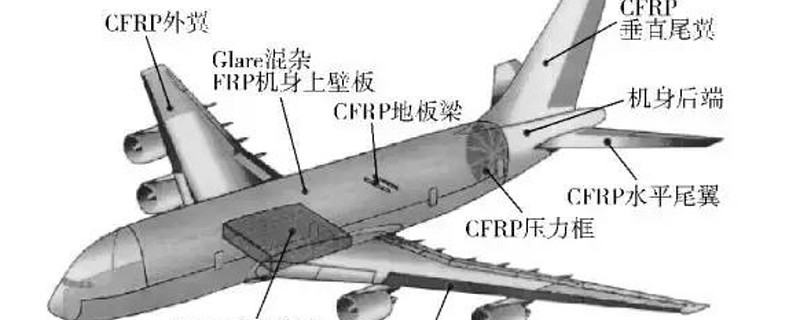
2. Key Performance Advantages
Performance Index | Technical Advantage |
---|---|
Specific strength and stiffness | Significantly higher than aluminum or steel; reduces weight by over 30% |
Fatigue and corrosion resistance | Suitable for harsh climates and repetitive loading cycles |
Thermal stability | Maintains dimensional accuracy in high-altitude environments |
Electromagnetic properties | Designable as radar-absorbing for stealth aircraft |
Lifecycle cost | Longer service life with lower maintenance costs |
3. Main Forming Processes
Sanse applies various advanced processes to meet the precision and strength requirements of aerospace-grade components:
- Automated Fiber Placement (AFP): Ideal for large skin structures with high-speed and precise layering
- Autoclave forming: Ensures interlaminar bonding quality for primary load-bearing parts
- Resin Transfer Molding (RTM): Suitable for complex medium-sized components
- Thermoplastic compression molding: Offers fast forming and reheating capabilities for efficient production
4. Typical Application Cases
1. Commercial Aircraft
Carbon fiber composites are extensively used in Boeing 787 and Airbus A350 to construct wings and fuselage sections, greatly enhancing fuel economy.
2. Military Fighter Jets
The F-35 and other advanced fighters utilize large amounts of carbon fiber for enhanced stealth and performance.
3. Aerospace and UAVs
Components like rocket fairings, satellite antenna arms, and drone frameworks rely heavily on high-modulus carbon fiber structures.
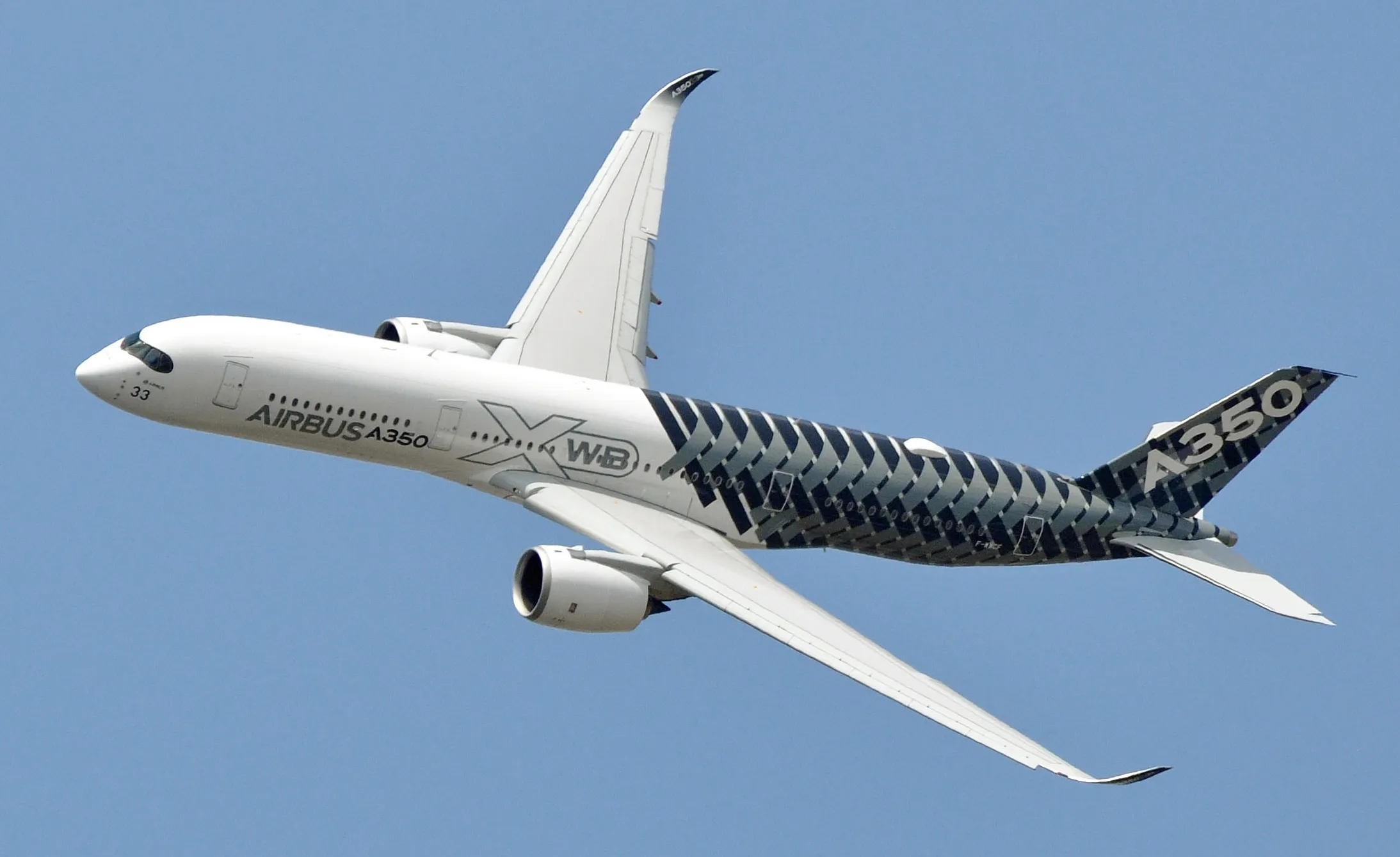
5. Sanse Advantages
- 20+ years of experience in composite manufacturing with aerospace-grade process control
- Independent mold design and customization for diverse specifications
- Flexible prototyping-to-production transition for R&D support
- International quality standards; trusted by aviation and military customers globally
6. Challenges and Future Trends
Despite their great potential, carbon fiber aerospace structures face challenges such as high material cost, complex structural design, and limited NDT (non-destructive testing) techniques. The future of development will focus on:
- Developing low-cost prepreg and rapid-cure resin systems
- Wider adoption of automated fiber placement and robotic forming
- Establishing green recycling mechanisms for composite waste
- Integration of smart forming and real-time monitoring technologies
Conclusion
At Sanse, we are committed to advancing composite technology and providing reliable carbon fiber solutions for the aerospace and high-end equipment industries. For more details about our aerospace composite capabilities, customization services, or partnership opportunities, please visit our official website cn-frp.net.