Application Analysis of FRP Automotive Exterior Parts and Bathroom Products
Fiberglass Reinforced Plastic (FRP) is a high-performance composite material that has been widely applied in automotive manufacturing, truck exteriors, modern bathrooms, kitchens, and industrial facilities in recent years. This article focuses on FRP automotive exterior parts, FRP truck exterior parts, FRP bathroom products, and FRP sinks to analyze their performance advantages, mainstream processes, and market application trends.
1. FRP Automotive Exterior Parts: An Ideal Choice for Lightweight and High Strength
FRP is increasingly replacing some metals and thermoplastics in automotive exterior applications due to its unique material properties:
- High strength and impact resistance to improve vehicle safety;
- Lightweight to reduce overall vehicle weight and improve fuel efficiency;
- Great design flexibility for personalized appearances;
- Corrosion-resistant and rust-proof, prolonging service life.
Common FRP automotive exterior parts include front and rear bumpers, grilles, spoilers, fenders, and body kits. These components are typically manufactured using SMC compression molding for high-volume production and precise surface control.
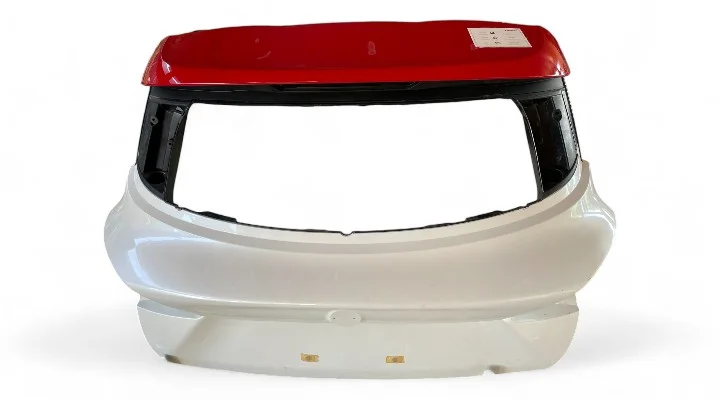
2. FRP Truck Exterior Parts: Combining Weather Resistance and Customization
Trucks operate in harsh environments, requiring exterior materials with higher durability. FRP offers excellent structural strength and resistance to UV rays and salt spray, making it suitable for long-term outdoor use.
Main applications include:
- Roof fairings and sunshades: improve aerodynamics and fuel efficiency;
- Side skirts and rear body kits: enhance vehicle aesthetics and brand image;
- Truck facias and lamp housings: support custom shapes and paint finishes.
Truck parts are often manufactured with high-strength steel molds and SMC/BMC compression processes, meeting both performance and small-batch customization needs.
3. FRP Bathroom Products: A Rising Star in Modern Interior Design
In modern bathroom design, FRP is widely used for bathtubs, washbasins, shower trays, and vanity cabinets. Advantages include:
- Waterproof and mildew-resistant, with long-lasting color stability;
- Easy to clean, with smooth surfaces resistant to stains;
- Luxurious texture, capable of replacing marble and artificial stone;
- Moderate cost, suitable for large-scale residential projects.
Especially in one-piece molded structures, hand lay-up FRP processes provide great design freedom for complex shapes.
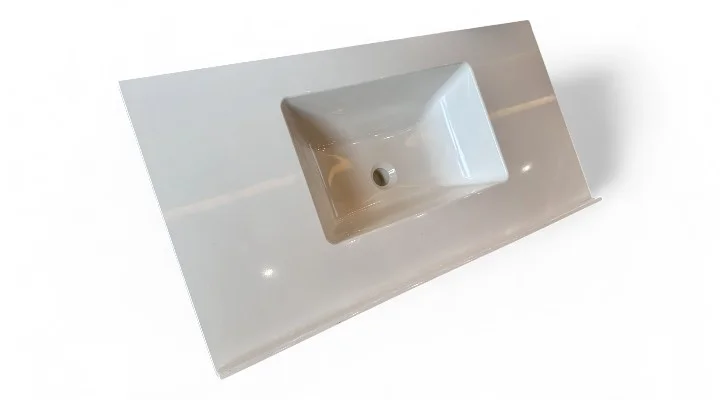
4. FRP Sinks: Ideal for Kitchens and Industrial Settings
FRP sinks are well-suited for home kitchens, commercial kitchens, laboratories, and hospitals, offering the following advantages:
- Acid and alkali resistance for chemical labs and food processing facilities;
- High strength and scratch resistance for durability;
- Support for various installation types (drop-in, top-mount, wall-mounted);
- Attractive appearance with customizable colors and shapes.
With the trend of integrated kitchen cabinetry, FRP sinks offer better integration and design consistency, making them an eco-friendly and functional material choice.
5. Molding Processes and Mold Support
Most of the above FRP products are manufactured using the following processes:
- SMC Compression Molding: ideal for mass production with consistent surface finish;
- RTM (Resin Transfer Molding): suitable for complex, high-performance parts;
- Hand Lay-up: high flexibility for custom and low-volume production.
High-quality molds are essential to FRP product success. Professional mold manufacturers like MDC Mould (Zhejiang MDC Mould Co., Ltd.) specialize in SMC, BMC, and composite material molds, offering high-precision molding solutions to ensure excellent structure and appearance of FRP components.
6. Future Trends and Industry Opportunities
With stricter environmental regulations and increased consumer demand for aesthetics and performance, FRP materials have a promising future in transportation, construction, and industrial equipment sectors. Especially in electric vehicle body panels, lightweight truck parts, and high-end customized bathroom systems, composite materials will play an even greater role.
From a manufacturing perspective, integrating digital mold design with automated compression systems will make FRP products more efficient, eco-friendly, and customizable.
Conclusion
The versatility and process adaptability of FRP materials make them an indispensable part of modern industry. Whether in FRP automotive exterior parts or FRP bathroom and sink products, their performance and market value are continuously rising. Understanding FRP industry trends and investing in smart manufacturing and high-end customization will be key to future development.