Why Are More UAVs Choosing Carbon Fiber Shells?
UAVs (Unmanned Aerial Vehicles), as representatives of intelligent aviation equipment, greatly depend on the selection of structural materials to determine their flight performance and mission efficiency. Under the requirements of lightweight, high strength, electromagnetic compatibility, and fatigue resistance, carbon fiber UAV shells and carbon fiber UAV components are gradually replacing traditional metals and engineering plastics, becoming the mainstream solution.
So, what are the core advantages of UAV composite material shells? How do lightweight UAV components achieve design breakthroughs through advanced composite technology? This article will comprehensively analyze this flight structure revolution from multiple dimensions: technology, processes, performance, and market trends.
What is Carbon Fiber Composite Material? Why Has It Become the First Choice for UAV Manufacturing?
Carbon fiber composite materials (CFRP) are composite structural materials formed by combining carbon fibers with resin matrices. They offer advantages such as low density (~1.6 g/cm3), high specific strength, good thermal stability, and strong corrosion resistance.
Compared to aluminum alloys or engineering plastics, CFRP exhibits significant advantages in impact resistance, fatigue life, and electromagnetic performance, making it particularly suitable for the structural design of flying vehicles that require high load-bearing capacity and extreme environmental adaptability.
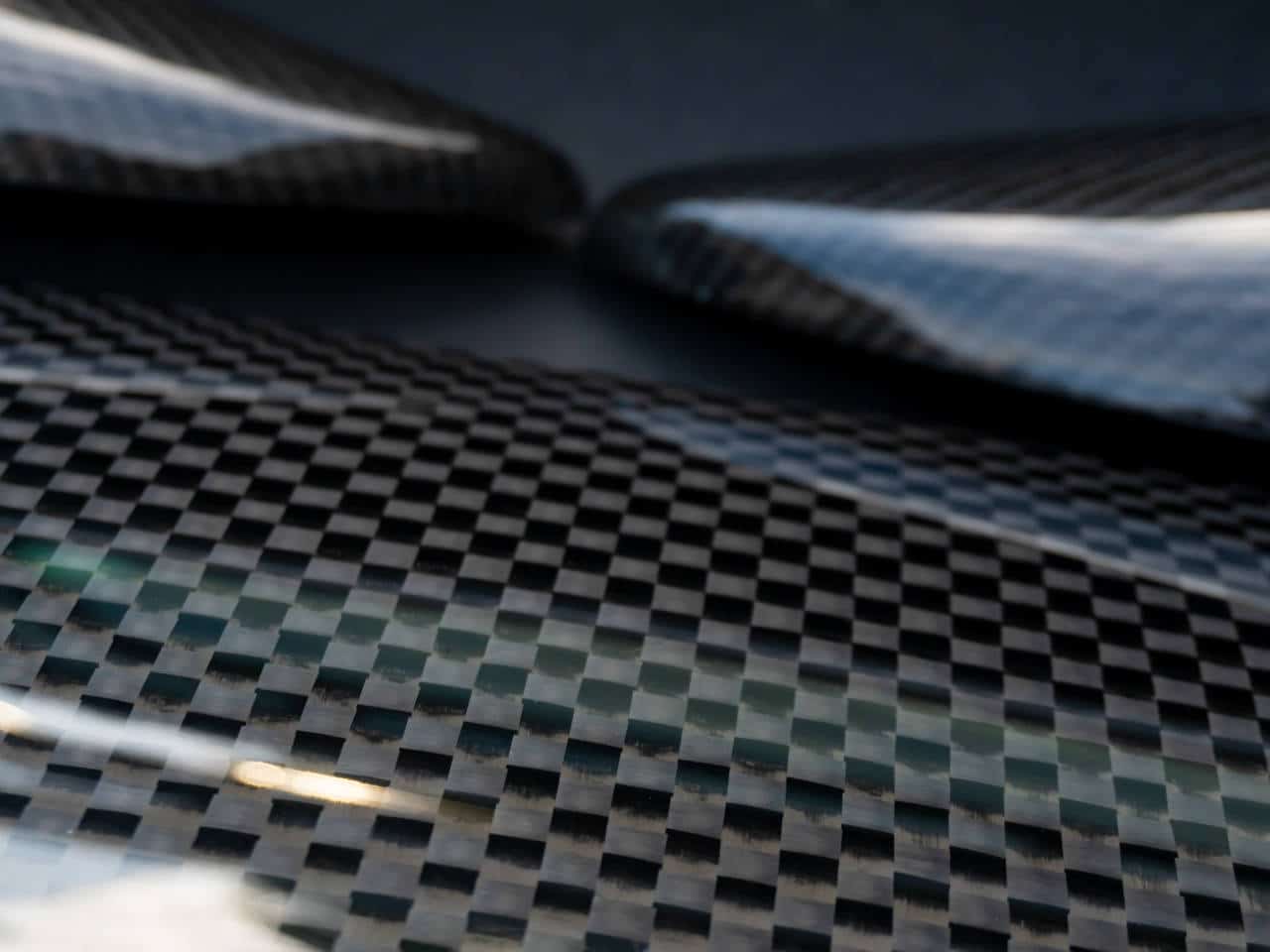
UAV Carbon Fiber Components: Lighter, Yet Stronger
The application of carbon fiber in UAVs is no longer limited to the shell; it now covers a wide range of parts from structural brackets to functional modules:
- Shell and Main Body: Achieving lightweight and high-strength protection for the overall framework of the aircraft.
- Rotor Blades and Propellers: Improving aerodynamic efficiency while reducing vibration and noise.
- Landing Gear and Mounting Brackets: Offering exceptional compressive strength and excellent dynamic load-bearing capacity.
- Communication/Radar Covers: Providing good electromagnetic transparency, suitable for integrating antennas or sensitive electronic devices.
Especially in high-end reconnaissance and attack UAVs, as well as logistics transport UAVs, high specific stiffness structural components have become the core of design, placing carbon fiber components in key positions.

How Are Lightweight UAV Components Manufactured? Revealing Core Processes
Achieving lightweight design not only depends on the materials themselves but is also closely related to advanced manufacturing processes. The current mainstream manufacturing methods for UAV carbon fiber components include:
- Compression Molding (SMC/BMC): Suitable for mass production of complex curved shell and structural panel components with high repeatability.
- Autoclave Molding: Used for high-performance composite structural components at the aerospace level, offering high internal density.
- Vacuum-Assisted Resin Infusion (VARI): Ideal for large structural components with excellent cost-performance ratio.
- Prepreg Layup + CNC Cutting: Suitable for small batch, highly customized UAV parts development.
By utilizing CAD/CAE analysis and topology optimization technologies, structural designers can further eliminate redundant structures, improving flight dynamics efficiency and unit payload utilization.
Composite Material Shell vs Metal Shell: Which is More Suitable for UAVs?
Performance Indicators | Carbon Fiber Composite | Aluminum Alloy | Engineering Plastics |
---|---|---|---|
Density | 1.6 g/cm3 | 2.7 g/cm3 | 1.2 g/cm3 |
Specific Strength | ★★★★★ | ★★★ | ★★ |
Fatigue Life | Extremely High | Medium | Low |
Corrosion Resistance | Excellent | Needs Treatment | Average |
Complex Structure Molding | Excellent (suitable for irregular shapes) | Poor | Average |
From a comprehensive performance perspective, UAV composite material shells excel in structural efficiency, aerodynamic performance, electromagnetic compatibility, and appearance customization, making them the first choice for future UAV structural components.
Future Trends in UAV Manufacturing: Modularization, Lightweight, and Intelligence
With the emergence of applications such as eVTOL (electric vertical takeoff and landing aircraft), unmanned cargo drones, and military reconnaissance platforms, the demand for composite material lightweight UAV components continues to grow. Future trends include:
- Automated Layup Robots + Digital Compression Molding: Improving composite material molding efficiency and consistency.
- Composite Materials + Embedded Sensors: Achieving structural status monitoring and intelligent maintenance.
- Integrated Structural Design: Reducing assembly parts, improving overall strength and sealing performance.
Conclusion: Why Choose Carbon Fiber UAV Shells Now?
Whether it's to enhance aircraft endurance, improve payload capacity, or break through durability barriers in complex mission environments, carbon fiber UAV shells and UAV carbon fiber components provide industry-leading solutions.
For UAV companies that pursue high performance, intelligent manufacturing, and long-term reliability, mastering composite material design and manufacturing capabilities is not only key to technological upgrades but also a future guarantee to win in the competitive market.