Automotive Composite Parts and Compression Molding Solutions for Lightweight Manufacturing
Introduction: The Inevitable Path Toward Lightweight Vehicles
With the rapid advancement of new energy vehicles, autonomous driving technologies, and global carbon neutrality goals, lightweight manufacturing has become a key focus for automakers. It not only enhances fuel efficiency and driving range but also supports safety and environmental objectives. Composite materials and compression molding technology are emerging as vital enablers of automotive lightweighting.
Composite Materials in Automotive Interior and Exterior Applications
While traditional steel offers structural strength, its heavy weight conflicts with modern lightweighting goals. In contrast, composite materials such as SMC, BMC, LWRT, FRP (fiberglass-reinforced plastic), and CFRP (carbon fiber-reinforced polymer) deliver high strength-to-weight ratios, corrosion resistance, and flexible design. These materials are widely applied in both automotive interior and exterior molding:
- Automotive Interior Molding: SMC/BMC/LWRT compression molding is used to mass-produce parts like instrument panel supports, door panels, seat backs, and roof liners, offering both structural integrity and comfort.
- Composite Automotive Exterior Parts: Components such as bumpers, fenders, wheel arches, and spoilers made with composite materials reduce vehicle weight and improve surface finish and impact resistance.
- FRP Automotive Exterior: Fiberglass-reinforced parts are ideal for complex exterior surfaces and are widely used in commercial and customized vehicles.
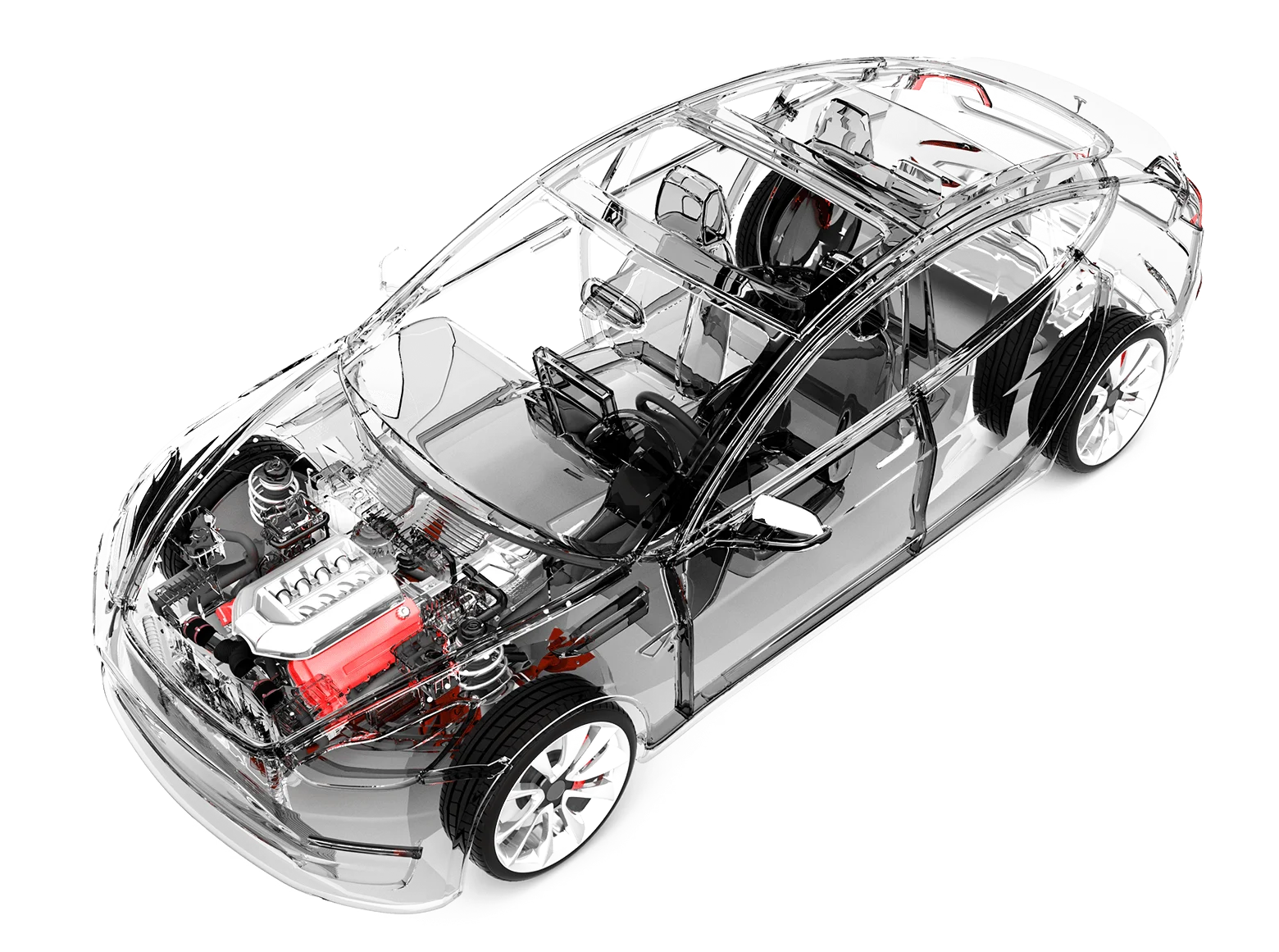
LWRT: The Ideal Material for Automotive Interiors
LWRT (Low Weight Reinforced Thermoplastics) is a type of thermoplastic composite that offers excellent acoustic performance, corrosion resistance, weatherability, and efficient processing. It is commonly used in car door panels, under-carpet structures, and trunk liners. LWRT automotive parts are lightweight, recyclable, and represent a sustainable approach to modern vehicle manufacturing.
Compression Molding: A Reliable, High-Efficiency Process
Compression molding is a key process in producing automotive composite parts. It offers high efficiency, superior mechanical properties, and excellent surface finishes—ideal for mass-producing large or structural components. Main advantages include:
- Short cycle times for high-volume, custom production
- High material utilization with minimal scrap
- Long mold life and high repeatability
- Compatibility with various composite systems (SMC, BMC, LWRT, etc.)
For automotive component molders, mastering advanced compression technology is essential for gaining competitive advantage.
Carbon Fiber Composites: A Symbol of High Performance
Carbon fiber automotive parts offer exceptional strength-to-weight ratios, heat resistance, and rigidity. These features make them popular in premium passenger vehicles, electric sports cars, and racing cars. Carbon fiber roofs, hoods, spoilers, and chassis shields not only reduce weight but also enhance aesthetics and brand value.
As carbon fiber costs continue to decline, its penetration in mid- to high-end production vehicles is expected to rise steadily.
New Trends in the Automotive Parts Supply Chain: Customization and Integration
In an era of multi-variant, small-batch, and fast iteration production, automakers demand more from their suppliers. Modern auto part suppliers are evolving from single-part providers to partners offering comprehensive and customized solutions:
- Custom Automotive Part Production: Tailored molding solutions based on vehicle platform, structural requirements, and material selection.
- OEM Parts Supplier: Deep involvement in early-stage design, engineering, and sample validation with car manufacturers.
- Composite Materials Partner: Offering full-process solutions covering material development, mold making, compression molding, post-processing, and assembly.
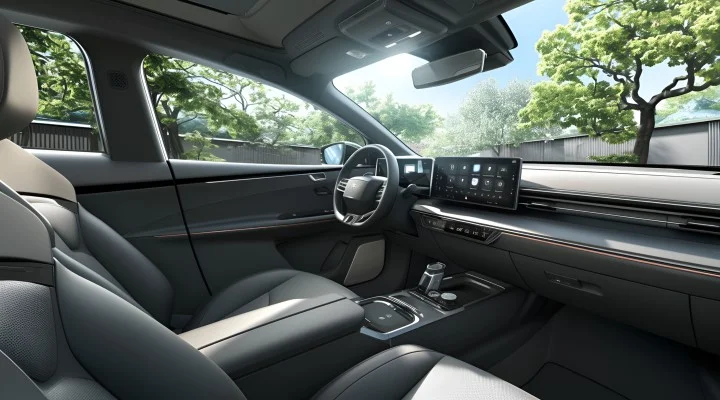
Lightweighting Solutions for Future Mobility
The future of mobility will be defined by lightweight, intelligent, electric, and sustainable vehicles. Composite materials and compression molding technologies provide a solid foundation for this transformation. From FRP exterior parts and LWRT interiors to carbon fiber chassis and custom structural parts, composite exterior and structural components are gaining a larger role in vehicle production.
As an automotive composite parts partner, companies with capabilities in material engineering, molding technology, and mass production will play a central role in the evolving global automotive supply chain.