Composite Electrical Boxes: Modern Solutions for Safety and Performance
With the rapid advancement of industrial automation and intelligence, traditional metal electrical boxes are gradually revealing their limitations in high-demand environments—such as poor corrosion resistance, weak insulation, and heavy weight. To overcome these challenges, composite electrical boxes have emerged. Among them, enclosures made of BMC (Bulk Molding Compound) have become a breakthrough in the field of electrical housings.
What is a Composite Electrical Enclosure?
A composite electrical enclosure is an electric protection housing made primarily from fiberglass-reinforced thermosetting plastic materials such as BMC or SMC, shaped through compression molding. These enclosures offer superior insulation and corrosion resistance compared to traditional metal alternatives, while also ensuring long-term stable operation in harsh environments.
Advantages of BMC Electrical Housing
- Excellent Insulation: Ensures safe operation of internal components, preventing leakage and short circuits.
- Corrosion & Aging Resistance: Ideal for chemical, coastal, and high-humidity environments.
- Lightweight: Greatly reduces installation costs and transportation complexity.
- High Strength & Impact Resistance: Offers reliable mechanical properties for both indoor and outdoor use.
- Environmentally Friendly: Non-toxic and emissions-free during manufacturing, aligning with green production standards.
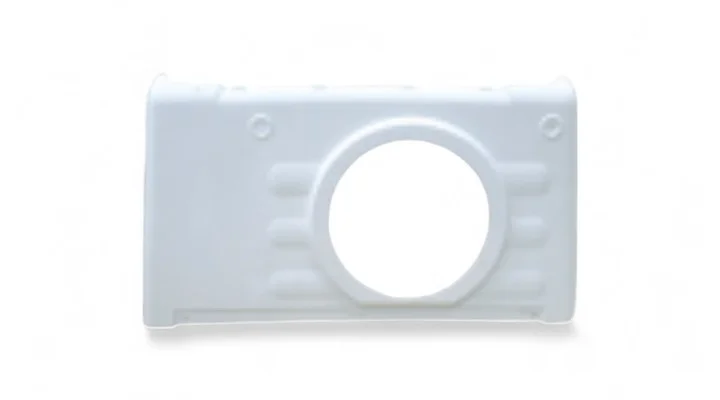
Explosion-proof Electrical Box Solutions
In hazardous locations such as petrochemical plants, mines, and pharmaceutical facilities, explosion-proof electrical boxes are critical for ensuring safety. Due to their inherent insulating and non-conductive properties, composite materials have become the new standard for explosion-proof electrical box design and manufacturing. Through specialized mold designs and structural reinforcement, these boxes can meet strict requirements for airtightness, explosion containment, and flame retardance.
Innovation in Electrical Box Design and Manufacturing
With the widespread adoption of 3D modeling and smart manufacturing, electrical box design and manufacturing is evolving toward customization, efficiency, and high performance. The formability of composite materials allows for the easy customization of complex structures, enhancing both appearance and functionality. Additional features like integrated rails, wiring modules, and display windows can further improve the user experience.
How to Choose a Reliable Electrical Box Manufacturer
Choosing an experienced and capable electrical box manufacturer is crucial to product quality. A qualified supplier should offer the following:
- Complete BMC/SMC compression molding equipment and quality testing systems;
- End-to-end capabilities from electrical box design to mold development and mass production;
- Custom services such as drilling, EMI shielding, and explosion-proof certification;
- Certifications such as ISO9001, UL, and other relevant quality systems.
Application Fields
Composite electrical boxes are widely used in the following areas:
- New Energy: PV inverter boxes, energy storage cabinets
- Rail Transit: Electrical control boxes for trains
- Telecommunications: Outdoor base station enclosures
- Municipal Engineering: Meter boxes, branch boxes
- Industrial Automation: Control cabinets, electrical junction boxes, and more
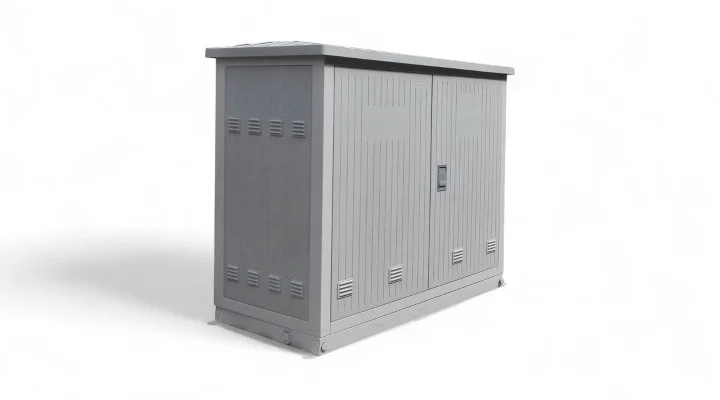
Conclusion
Composite electrical boxes are indispensable in modern electrical systems. Their advantages in safety, durability, lightweight construction, and eco-friendliness are making them ideal replacements for traditional metal boxes. Particularly in the field of explosion-proof electrical boxes, the use of BMC material offers a more reliable solution for hazardous environments. As manufacturing technologies evolve and market demand grows, electrical box design and manufacturing will continue progressing toward high-performance, customizable, and smart green solutions.