Composite Car Doors and Body Panels: PHC Materials and Mold Design | High-Performance Composite Molding
As the global automotive industry shifts toward lightweighting, environmental protection, and high performance, composite materials are playing an increasingly vital role in vehicle manufacturing. Among these, composite car doors and composite body components have become key parts for implementing lightweight strategies. Emerging materials such as PHC composites have also demonstrated excellent performance in mass production. Meanwhile, composite mold design has become critical to achieving high-efficiency, high-quality manufacturing.
I. Composite Car Doors: A Breakthrough in Automotive Lightweighting
1.1 Performance Advantages of Composite Car Doors
Compared with traditional steel car doors, composite car doors offer significant benefits in the following aspects:
- Lightweight: Weight reduction of 30%~50%, significantly lowering overall energy consumption.
- Corrosion Resistance: Glass or carbon fiber reinforcements inherently offer excellent corrosion resistance.
- Thermal and Acoustic Insulation: Low thermal conductivity improves NVH performance.
- Integrated Design: Enables one-piece molding of inner panels and reinforcements, reducing part count.
1.2 Forming Process Analysis
The current mainstream processes are SMC compression molding and thermoplastic compression molding, both suitable for mass production. For complex structures or higher-performance requirements, carbon fiber-reinforced thermoset composites are used, typically formed via compression or prepreg molding processes.
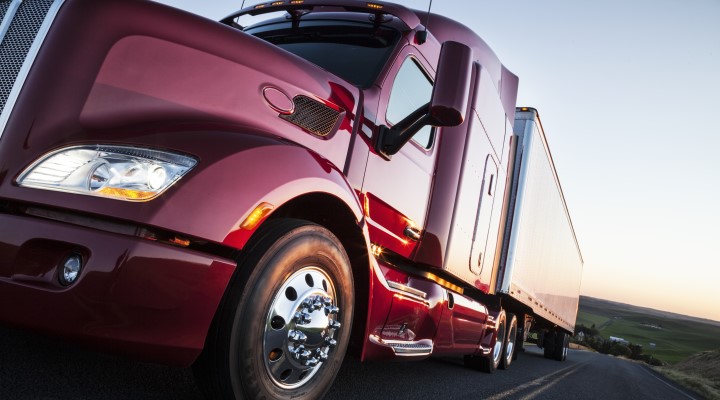
II. PHC Composites: A New Generation High-Performance Material Platform
2.1 Introduction to PHC Composites
PHC (Press Hardened Composite) is a composite system composed of thermoset resin matrix and high-modulus reinforcing fibers. It combines structural strength and molding efficiency, making it ideal for manufacturing high-strength structural automotive parts.
- High Strength and Rigidity: Meets regulations for side-impact and roof crush resistance.
- Excellent Flowability: Suitable for filling molds with complex geometries.
- Compatible with compression molding: Easily integrates with existing SMC mold systems.
2.2 Automotive Applications of PHC
PHC is currently used in:
- Door inner panels: Provides structural integration while meeting strength requirements.
- Bumper beams: Replaces steel parts for significant weight reduction.
- EV battery pack bottom shields: Excellent impact resistance and flame retardancy.
For example, a luxury vehicle using PHC instead of steel in its door inner panel achieves a weight reduction of 4.2 kg, while also improving side-impact performance and helping meet higher safety standards.
III. Composite Mold Design: The Core of Efficient Molding
3.1 Key Considerations in Mold Design
Considering the molding characteristics of composites, mold design must address the following elements:
- Resin Flow Paths: Optimize gate layout to avoid voids and dry spots.
- Demolding Structure: Apply proper draft angles and surface treatments (e.g., electroless nickel plating).
- Temperature Control Systems: Enable rapid heating and precise cooling cycles.
- Vacuum Assist Systems: Enhance degassing efficiency, especially in PHC and carbon fiber molding.
3.2 Mold Materials and Processing
Common mold materials include:
- P20 tool steel: Suitable for thermoset materials such as SMC and BMC.
- H13 steel: High wear resistance and suitable for high-temperature molding.
- High-strength aluminum alloys: Applied in thermoplastics, offering excellent thermal conductivity.
Precision processing is achieved through 5-axis CNC machining, EDM, and mirror polishing. Molding simulations using software such as Moldflow are used to optimize the process.
IV. Expanding Applications of Composite Body Components
Beyond car doors, composites have been widely adopted in various automotive body structural components:
Component | Common Materials | Key Advantages |
---|---|---|
Engine Hood | SMC / CFRP | Lightweight, high strength |
Trunk Lid | SMC / GMT | High forming efficiency, rigidity |
Car Roof | PHC / Carbon Fiber | Lower center of gravity, improved handling |
Side Structures | SMC + Metal Hybrid | Multi-material integration, meets crash standards |
4.1 Future Trends
- Integrated Design: Use of composites to form large integrated structures.
- Automated Compression Lines: Improve takt time and reduce cost.
- Recyclable Composites: Driving sustainable manufacturing.
- Thermoplastic-Thermoset Hybrids: Balance rigidity, ductility, and weldability.
Conclusion: Driving Systemic Transformation in Composite Vehicle Manufacturing
Composites are expanding from non-structural parts to core structural body components. The application of PHC composites and efficient mold design have brought reliable molding solutions to the industry. Amid the wave of vehicle electrification and smart mobility, composite technologies will become the foundation for next-generation vehicle platforms. Manufacturers should focus on the integration of materials, molds, and processes to seize innovation opportunities and enhance core competitiveness.