Compression Molding: Development Trends and Industry Outlook
1. Basic Principles of Compression Molding
Compression molding is a technology that uses high temperature and high pressure to form plastic, rubber, and other materials. This process is widely used to produce complex-shaped, high-precision parts, particularly in industries that require large-scale production. Compression molding not only ensures high-quality parts but also maintains production efficiency and consistency.
The operation process of compression molding includes: material heating, insertion into molds, applying pressure to form, and cooling and demolding. The precise control of each step ensures the final product meets quality standards.
2. Applications of Compression Molding Technology
1. Automotive Industry
In the automotive industry, compression molding is widely used to produce parts like car shells, bumpers, dashboards, and more. Automotive parts require high strength, wear resistance, and corrosion resistance, and compression molding ensures the precision and consistency of each part, as well as high production efficiency.
2. Electronics Industry
In the electronics industry, compression molding is used to manufacture various electronic housings, circuit board supports, connectors, and other components. Compression molded parts offer excellent electrical insulation properties and strong mechanical strength, making them suitable for harsh operating environments.
3. Home Appliance Industry
In the home appliance industry, compression molding is often used to produce various appliance housings and internal components, such as TV housings, washing machine parts, and more. This technology ensures the stability of quality during mass production while maintaining good mechanical properties.
4. Construction Materials Industry
In the construction industry, compression molding is used to produce building materials such as wall panels, flooring, ceiling panels, and more. Compression molding ensures that these parts retain high strength and excellent surface quality even when produced in large sizes or with complex shapes, making it an essential manufacturing technology in modern construction.
5. Aerospace and Military Industries
The aerospace and military industries require parts with extremely high strength, heat resistance, and reliability. Compression molding, by using composite materials, is widely applied in these fields, especially in the production of aircraft shells, missile parts, and other high-strength components, providing superior solutions for demanding applications.
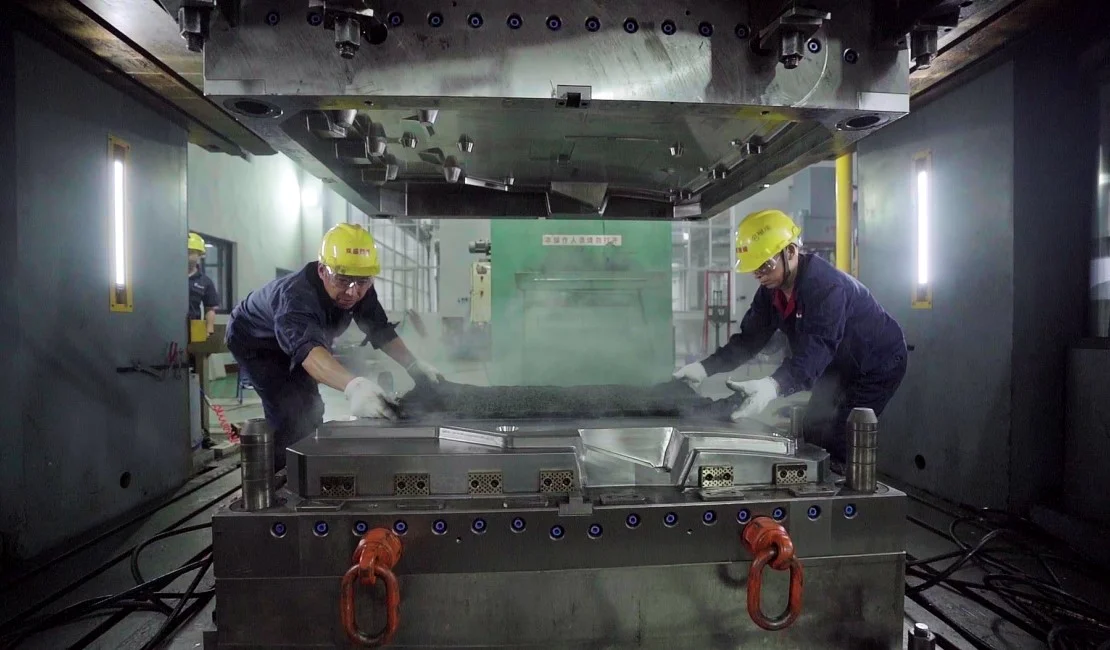
3. Advantages of Compression Molding Technology
1. High Production Efficiency
Compression molding allows for the mass production of parts, with high consistency and quality for each part. Compared to other molding processes, compression molding significantly improves production efficiency, making it especially suitable for producing large quantities of components.
2. High Precision and Consistency
Compression molding produces high-precision and dimensionally consistent parts. Because of its high forming precision, it is especially suitable for components that require strict control of dimensions and surface quality, such as automotive exteriors and electronic parts.
3. Strong Adaptability
Compression molding is suitable for various thermosetting and thermoplastic materials. It can meet the needs of different industries and produce complex components in various shapes and sizes.
4. High Material Utilization
Compression molding minimizes material waste by accurately placing the material, thereby improving material utilization and reducing production costs.
5. Energy-Efficient and Environmentally Friendly
Compared to traditional casting processes, compression molding has lower energy consumption and produces fewer emissions and waste, making it more environmentally friendly. The use of recyclable materials and green processes further enhances the eco-friendliness of compression molding technology.
4. Development Trends of Compression Molding Technology
1. Intelligent Production
With the advancement of Industry 4.0, the production of compression molding will gradually become intelligent. Automation control systems, machine learning, and artificial intelligence will be widely applied in mold design, production scheduling, and quality monitoring, improving production efficiency and product quality.
2. Green and Sustainable Manufacturing
Compression molding will focus more on eco-friendly production. The use of green materials, energy-saving equipment, and optimized processes will be key development directions for compression molding technology, promoting its sustainable development.
3. Application of New Materials
With the continuous emergence of new composite and high-performance materials, compression molding technology will be further expanded in high-tech fields such as aerospace, electric vehicles, and automotive lightweighting. The introduction of new materials will drive technological innovation and development in compression molding.
4. Innovation in Mold Technology
With ongoing advances in mold manufacturing technology, molds will become more precise and durable. Future molds will be able to meet the needs of more complex product requirements, driving the efficient production of compression molding technology.
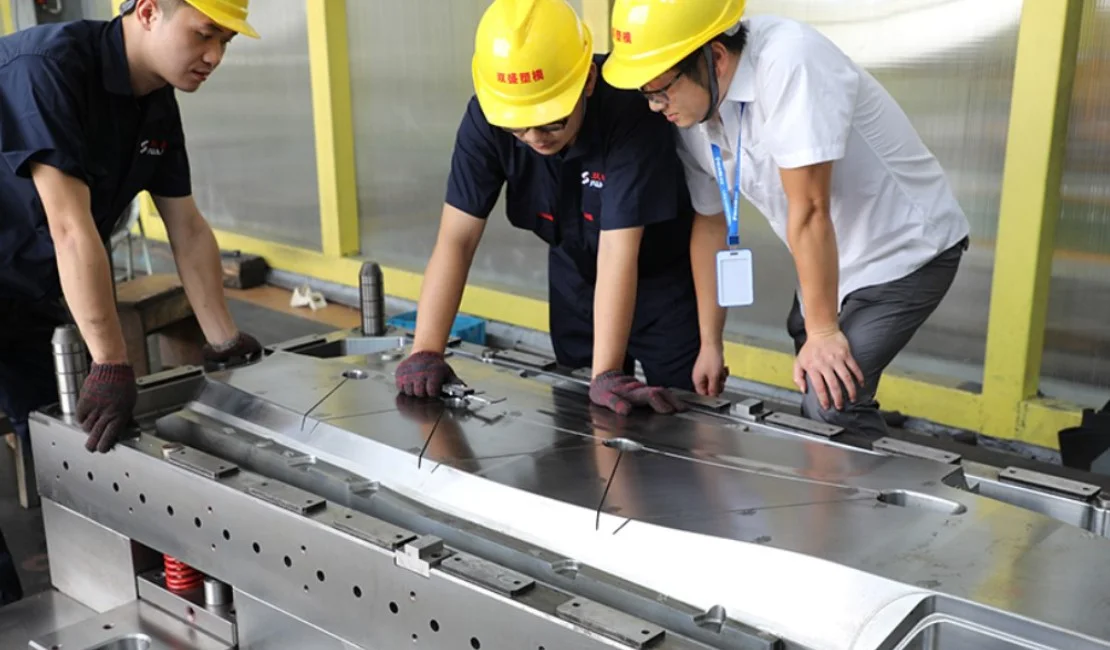
Conclusion
As an efficient, precise and widely applicable molding technology, molding process plays an important role in many industries. With the continuous progress of technology, molding process will show a broader development prospect in intelligent, green production and new material application. Whether in the automotive, electronics, home appliances or construction industries, the application of molding process will promote the innovation and development of related fields, and bring greater competitive advantage for enterprises.