LWRT Molds: Analysis of Lightweight Reinforced Thermoplastic Composite Forming Technology
1. Overview of LWRT Molds
LWRT (Low Weight Reinforced Thermoplastics) is a high-performance composite material widely used in automotive interiors, rail transit, and aerospace. LWRT molds are specifically designed for the forming process of LWRT materials, meeting the requirements of lightweight, high strength, and sound and thermal insulation, providing efficient and eco-friendly solutions for modern manufacturing.
2. Advantages of LWRT Materials
- Lightweight: LWRT materials have low density, significantly reducing product weight compared to traditional metal materials.
- High Strength: Reinforced fibers enhance impact resistance and fatigue performance, ensuring the longevity of the mold.
- Sound Absorption and Noise Reduction: LWRT features a porous structure that effectively absorbs noise, making it ideal for automotive carpet padding and engine hood insulation layers.
- High Temperature Resistance: LWRT molds are suitable for high-temperature forming processes, ensuring material stability in harsh environments.
- Recyclability: LWRT materials can be recycled, making them more environmentally friendly than thermosetting composites, in line with green manufacturing trends.
3. Design and Manufacturing of LWRT Molds
3.1 Mold Material Selection
LWRT molds are typically made from high-strength steel or aluminum alloy to ensure resistance to high temperatures and pressures while maintaining long-term stability. The mold surface undergoes special treatments such as chromium plating and nitriding to enhance wear resistance and demolding performance.
3.2 Optimization of Mold Cavity Structure
- Optimizing runner design to ensure uniform filling of LWRT materials and reduce stress concentration.
- Utilizing CAE simulation technology to improve molding accuracy and stability.
- Reasonably arranging cooling channels to enhance heat exchange efficiency and accelerate production cycles.
3.3 Adaptation to Forming Processes
The primary forming methods for LWRT include compression molding and vacuum forming:
- Compression Molding: Preheated LWRT material is placed into the mold and formed under high pressure, suitable for mass production while ensuring dimensional accuracy.
- Vacuum Forming: Negative pressure is used to form the material, ideal for producing large and complex structural parts with increased manufacturing flexibility.
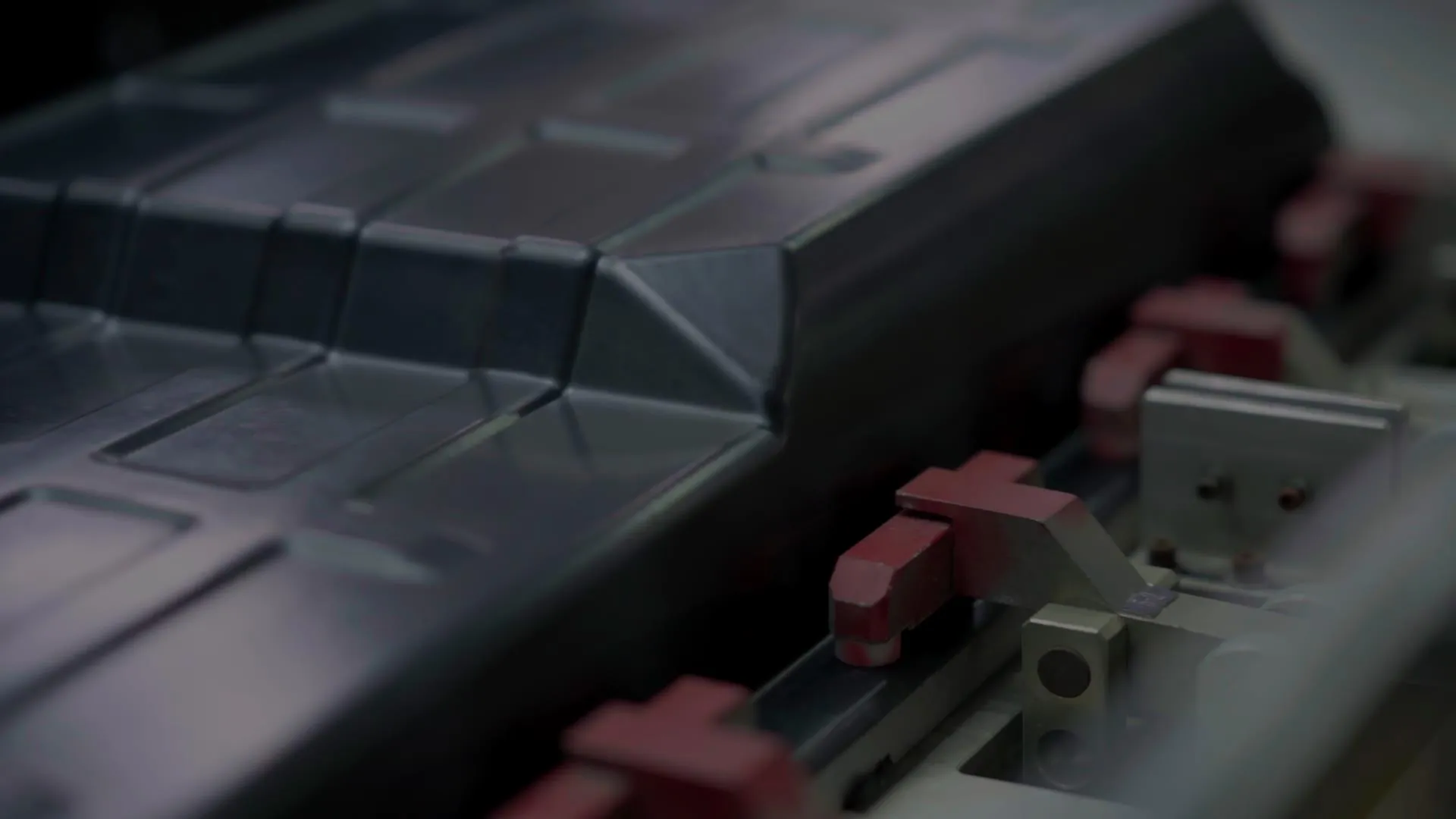
4. Application Fields of LWRT Molds
4.1 Automotive Industry
- Automotive Interiors: Door panels, dashboards, and trunk covers with lightweight designs to improve fuel efficiency.
- Engine Hood Insulation Layer: LWRT materials maintain stable performance in high-temperature environments, enhancing safety.
- Underbody Shields: Increased impact resistance extends the lifespan of vehicles.
4.2 Rail Transit
LWRT materials are widely used in rail transit applications such as train cabin interiors and seat frames, reducing train weight and improving operational efficiency.
4.3 Aerospace
Used for aircraft cabin insulation panels and door linings, providing high strength and lightweight advantages to reduce fuel consumption.
5. Future Trends in LWRT Mold Development
- Intelligent Design: AI simulation optimization to improve molding accuracy and reduce material waste.
- Green Manufacturing: Development of recyclable LWRT materials to promote sustainability.
- High-Efficiency Production: Innovative forming processes to reduce energy consumption and enhance production efficiency.
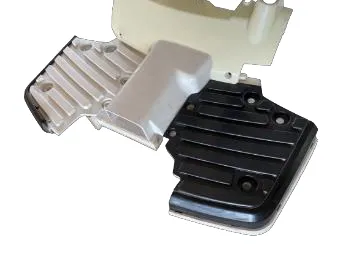
6. Conclusion
LWRT molds are the key technology for forming lightweight reinforced thermoplastic composite materials (LWRT), playing a crucial role in the automotive, rail transit, and aerospace industries. With continuous advancements in new material technologies and manufacturing processes, LWRT molds will offer broader application prospects in lightweight and high-performance manufacturing, providing more efficient and environmentally friendly solutions for the industry.