Comprehensive Analysis of SMC Molded Parts and SMC Composite Material Manufacturing
1. Definition of SMC Molded Parts
SMC (Sheet Molding Compound) molded parts are products made from SMC composite materials through the compression molding process. This material, based on unsaturated polyester resin, glass fiber, and fillers, boasts excellent mechanical properties, corrosion resistance, and electrical insulation properties.
2. SMC Composite Material Manufacturing Process
The manufacturing process of SMC composite materials includes the following key steps:
- Raw Material Preparation: Resin, glass fiber, fillers, and other additives are accurately measured according to the formulation to ensure stable material performance.
- SMC Sheet Preparation: Specialized equipment is used to evenly coat the resin mixture on a film, lay the glass fiber, and cover it with another layer of film to form a continuous sheet material.
- Maturation Process: After sheet preparation, the material needs to be cured in a constant temperature environment to ensure good flowability and molding performance.
- Compression Molding: The cut SMC sheet is placed in a heated compression mold, where it undergoes heating and pressure to form the desired product.
- Post-Processing and Inspection: After molding, the product requires trimming, grinding, coating, and dimensional inspection to ensure quality standards are met.
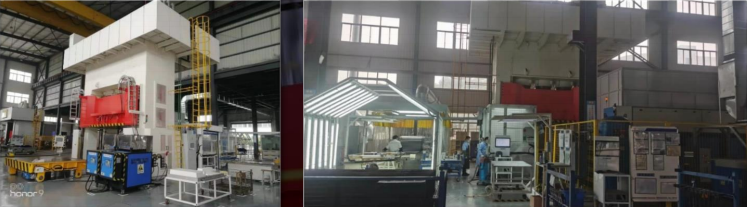
3. Performance Characteristics of SMC Molded Parts
- Excellent Mechanical Properties: SMC composite products have high strength and rigidity, capable of withstanding significant impact and mechanical loads.
- Outstanding Corrosion Resistance: SMC molded parts are highly resistant to acids, alkalis, and solvents, making them ideal for automotive exterior parts and industrial equipment housings.
- Superior Electrical Insulation: SMC composite materials provide excellent electrical insulation properties, widely used in electrical equipment and power systems.
- Lightweight Design: SMC molded parts have low density, reducing product weight and improving energy efficiency.
4. Application of SMC Molded Parts in the Automotive Industry
SMC molded parts are widely used in the automotive manufacturing sector, especially in body components and exterior parts:
- Body Structural Components: Such as engine hoods, trunk lids, fenders, and door inner panels, offering excellent impact resistance.
- Exterior Parts: Such as roof covers, front and rear bumpers, and spoilers, meeting both aesthetic and functional requirements.
- Battery Enclosures and Structural Components: SMC composite materials are extensively used in EV battery enclosures and battery box covers, ensuring safety and lightweight design.
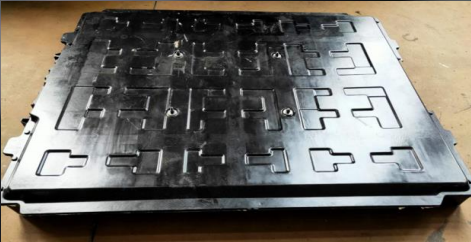
5. Advantages of SMC Composite Exterior Parts
- Excellent Surface Finish: SMC composite materials can achieve high gloss and complex curved structures through molds, meeting aesthetic requirements for exterior parts.
- UV Resistance: SMC exterior parts exhibit outstanding aging resistance, maintaining stable color and appearance even after prolonged outdoor exposure.
- Lightweight and Eco-friendly: With lower density, SMC materials reduce vehicle weight, helping improve fuel efficiency and lower carbon emissions.
6. Development Trends of SMC Molded Parts
As lightweight and eco-friendly concepts gain popularity, the market demand for SMC molded parts continues to grow. Future development will focus on the following aspects:
- Material Modification: By enhancing with nanomaterials and optimizing fiber structures, the mechanical properties and weather resistance of SMC products will improve.
- Intelligent Manufacturing: The introduction of automation equipment and digital control systems will enhance the efficiency and precision of SMC molded parts production.
- Eco-friendly Formulations: The use of eco-friendly resins, halogen-free flame retardants, and other materials will further reduce pollution during production.
7. Conclusion
With its superior performance, extensive application areas, and eco-friendly advantages, SMC molded parts are becoming vital in the automotive, construction, and electrical industries. As material technologies and molding processes continue to advance, the market prospects for SMC molded parts will become even broader.