Ford Bronco Hardtop Is Not "Cardboard": Composite Molding Technology Ensures Safety and Performance
In recent years, the rugged off-road SUV segment has surged in popularity in the Chinese market. Among them, the domestically produced Ford Bronco has drawn significant attention. This classic American-style off-roader, known for its high off-road capability and customizability, officially launched in China in 2024, sparking heated discussions among enthusiasts and industry media alike.
However, the emerging claim that it features a "cardboard roof" has raised concerns among some consumers regarding the safety of the removable Bronco hardtop. In fact, such worries stem more from a lack of understanding of composite structures and compression molding processes. This article delves into the technical aspects of the hardtop's SMC composite compression molding, highlighting its advantages in safety, weather resistance, comfort, and localized production quality — revealing the truth and clarifying the misunderstanding.
Removable Hardtop: Structural Advantages of High-Performance Composites
The Bronco's domestically produced hardtop features a three-piece removable design, greatly enhancing its flexibility and customization options. To balance strength and weight, Ford partnered with mold manufacturers to adopt SMC (Sheet Molding Compound) composite compression molding technology.
Key benefits include:
- High strength and rigidity: Excellent impact resistance, capable of withstanding structural stress in extreme off-road conditions.
- Weather resistance: Maintains stable physical properties under long-term exposure to heat, UV, and humidity.
- Corrosion resistance: Non-metallic, rust-free, and more durable than traditional metal roofs.
- Superior insulation and noise reduction: Enhances ride comfort by reducing wind noise and thermal radiation.
User feedback indicates that the SMC hardtop offers significantly better acoustic performance than traditional metal roofs, with a low-frequency, solid knocking sound typical of composites — far from the so-called "cardboard" feel.
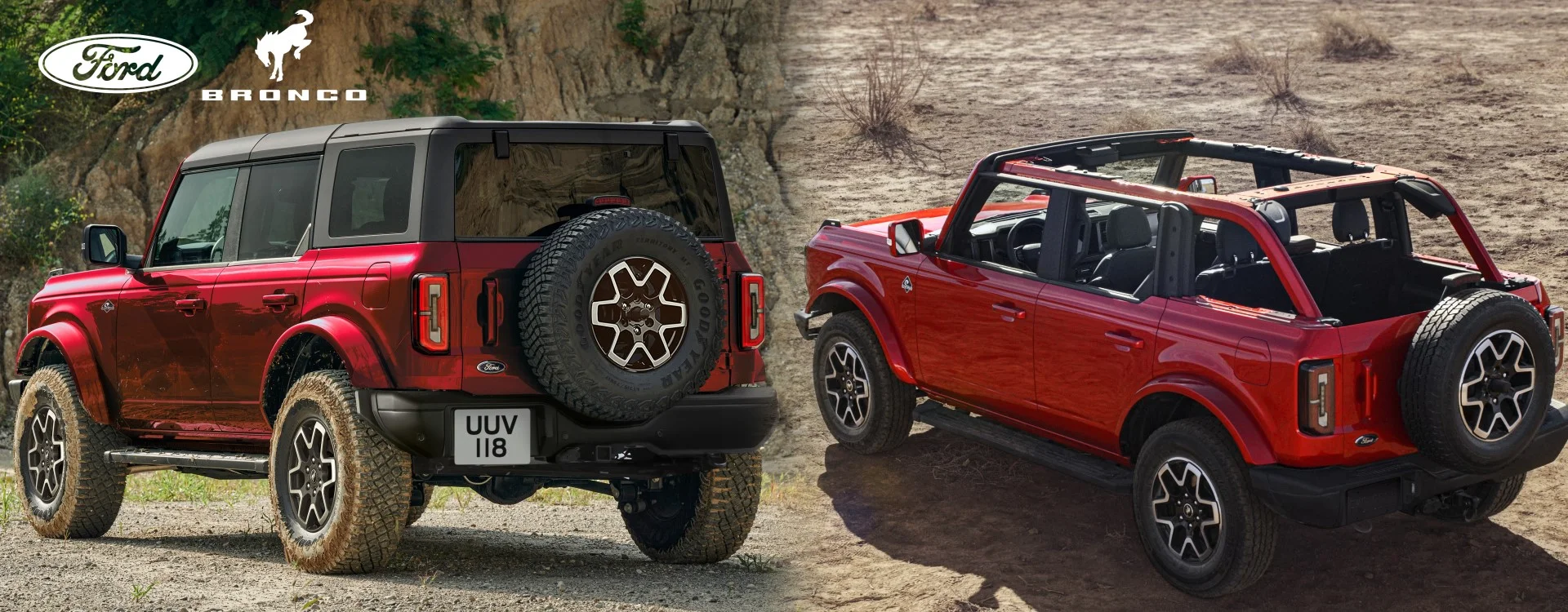
Compression Molding: Achieving Class-A Surface and Integrated Structure
Unlike traditional metal parts that require multiple welding and assembly steps, SMC compression molding uses high-pressure and high-temperature one-shot molding to deliver:
- Class-A surface quality, meeting OEMs' strict visual appearance standards;
- High molding precision, ensuring consistent dimensions across all parts;
- Support for structural rib designs, enhancing torsional rigidity and stability;
- Reduced post-processing, lowering overall manufacturing cost.
Sanse Manufacturing: Ensuring Quality and Consistency in Mass Production
The Bronco’s removable hardtop molds were supplied by Sanse Mould Technology, a leading Chinese mold manufacturer with rich experience in composite compression molding. From product design, flow analysis, and demolding optimization to trial production, Sanse worked closely with Jiangling Ford to ensure that the product not only meets performance standards but also maintains stability in mass production.
During validation, the hardtop passed global environmental aging tests, high-strength torsional simulations, and high-speed water impact simulations, complying with Ford's global quality standards.
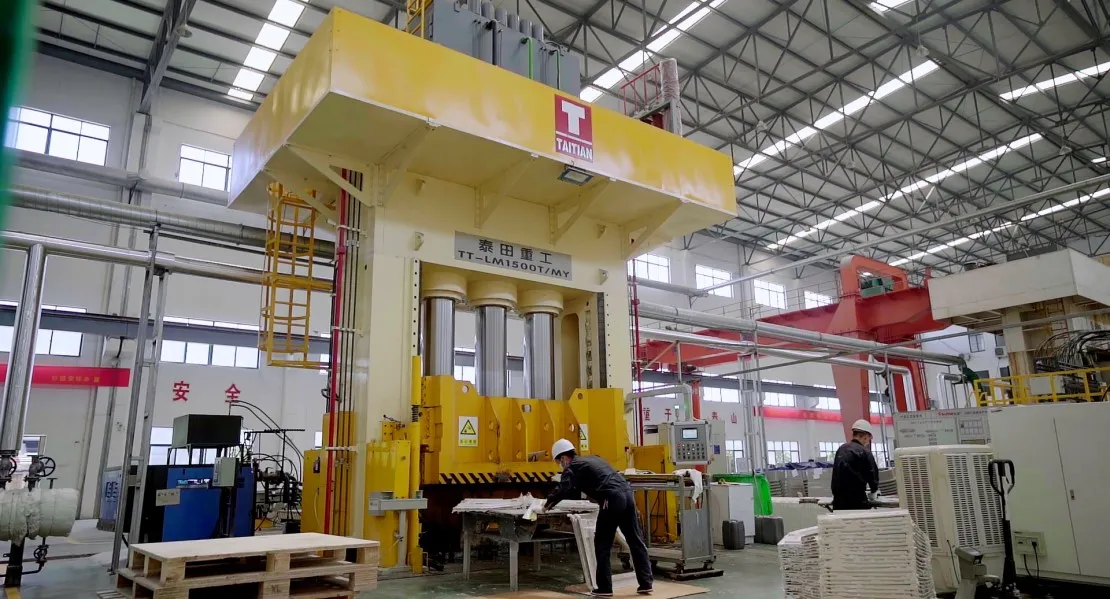
Composite Material Trends: Widely Used in Aerospace, Automotive, and Rail Transit
Composites are far from being "cheap plastic" — they are advanced materials composed of polymers reinforced with glass fiber, carbon fiber, and other additives. They are widely applied in:
- Aerospace structural components, radomes, and interior panels;
- Train car bodies and seat shells in rail transit;
- EV battery covers and door inner panels;
- Engine hoods and roof panels of premium cars such as BMW and Mercedes-Benz.
In modern industrial applications requiring high strength, lightweight, and durability, composite materials have become indispensable.
Market Feedback: Real-World Validation from Users
Since the Ford Bronco’s launch in China, user experiences with its removable hardtop have been overwhelmingly positive:
- Outstanding acoustic insulation, excellent sealing with no leakage;
- Good thermal insulation — slower cabin heat-up compared to metal roofs;
- Easy disassembly — three-piece structure manageable by a single person;
- Premium appearance — smooth surface with high-quality paint finish.
Conclusion: From Controversy to Mainstream — Technology Speaks Louder
From being misunderstood as “cardboard,” to delivering exceptional performance in structural safety, weather resistance, and comfort — the removable hardtop of the Ford Bronco is a textbook example of mature composite molding technology in the automotive industry. It is not only a major highlight in the localization of the Bronco in China but also signifies the advancement of China's automotive manufacturing toward high performance, efficiency, and quality.
As materials like SMC and CFRP continue to evolve, more key structural components will move away from traditional metals. Consumers should embrace these innovations with a rational mindset, welcoming a smarter, safer, and greener mode of transportation.