PHC Material Molding and Composite Material Applications
What is PHC Material?
PHC material (Poly-Hybrid Composite) is an innovative composite material that combines the advantages of both thermoplastic and thermosetting materials. PHC materials typically consist of reinforcing fibers (such as glass fibers, carbon fibers, etc.) and various resin matrices (such as polyester resin, epoxy resin, etc.). By precisely designing the material, PHC materials provide high strength, rigidity, heat resistance, and chemical resistance.
Advantages of PHC Materials
- High Strength and Rigidity: PHC materials offer excellent tensile strength and impact resistance through the use of reinforcing fibers, making them suitable for high-strength applications.
- Lightweight: PHC composites have a lower density compared to metals, providing excellent lightweight benefits, ideal for automotive industries to improve fuel efficiency.
- High Temperature and Corrosion Resistance: PHC materials maintain good performance under extreme environmental conditions, making them ideal for high-temperature and corrosive environments.
- Good Processability: PHC materials are easy to process via molding techniques such as compression molding and injection molding, making them ideal for mass production.
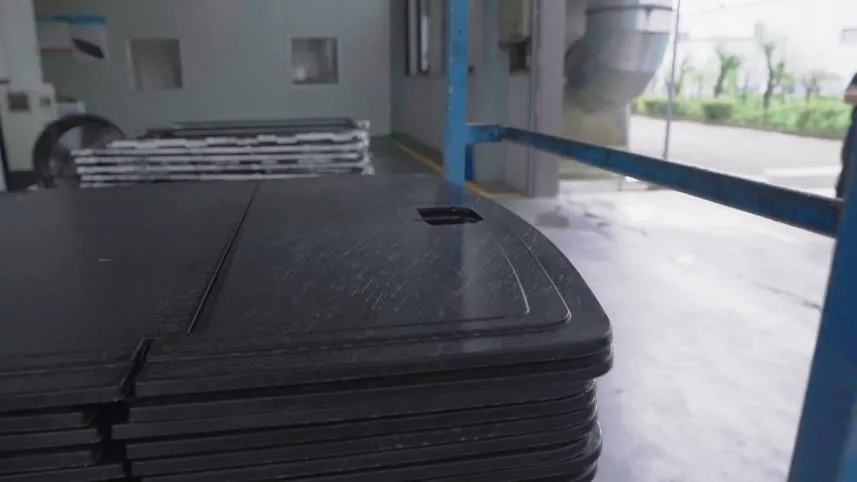
PHC Material Molding Process
PHC material molding is a process where PHC composites are heated and pressed in molds. This process is commonly used to produce complex-shaped and precise composite parts on a large scale. The main advantages of this molding process include:
- High Precision Molding: PHC materials retain high precision during the molding process, ensuring that the produced parts meet strict dimensional requirements.
- High Efficiency: The molding process allows for the rapid production of large volumes of parts, making it ideal for efficient mass production and reducing per-unit production costs.
- Energy Efficient and Environmentally Friendly: Compared to traditional metalworking, PHC material molding consumes less energy and produces less waste during production, aligning with green manufacturing principles.
- Complex Shape Manufacturing: The PHC molding process can handle complex geometric shapes, making it suitable for a variety of part designs.
Applications of PHC Materials
PHC materials are widely used across various industries due to their excellent properties, particularly in applications where lightweight, strength, and corrosion resistance are crucial. Some of the key application areas for PHC materials include:
1. Automotive Industry
PHC materials have extensive applications in the automotive industry, especially in automotive interior components and structural parts. With excellent lightweight characteristics, PHC materials can effectively reduce vehicle weight and improve fuel efficiency. Common automotive components made from PHC materials include door panels, dashboards, and seat frames.
2. Aerospace Industry
PHC composites are increasingly being used in the aerospace industry, especially in both internal and external aircraft structures. These materials provide excellent strength and rigidity while maintaining a low weight, making them ideal for aerospace components.
3. Electronics
PHC materials are also used in electronic products, particularly in housings and structural parts. With excellent electrical insulation properties and high-temperature resistance, PHC materials provide robust protection and attractive designs for electronic products such as smartphones and tablets.
4. Construction Industry
PHC materials are used in the construction sector, especially in window frames, door frames, and flooring. Thanks to their durability and corrosion resistance, they can withstand harsh environmental conditions, making them ideal for building exteriors.
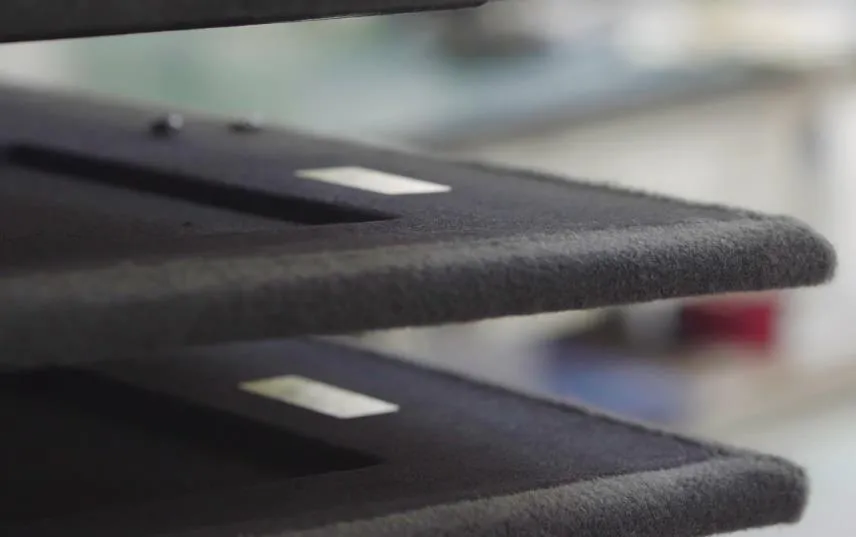
PHC Automotive Interior Components
Automotive interior components are essential for the vehicle’s comfort, aesthetics, and performance. PHC materials, due to their high strength, rigidity, and heat resistance, are widely used in the production of automotive interior parts. Common automotive interior components made from PHC materials include:
- Dashboard: PHC composites provide the required strength to support the dashboard structure, while their UV resistance ensures that the dashboard maintains its color even after prolonged exposure to sunlight.
- Seat Frame: The lightweight properties of PHC materials help reduce the overall weight of the car, enhancing fuel efficiency and driving performance.
- Door Lining: PHC materials can be used for door linings, providing impact resistance and reducing the overall weight of the door assembly.
SMC-PHC One-Piece Molding Technology
SMC-PHC one-piece molding technology involves combining PHC composites with SMC (Sheet Molding Compound) materials in the same mold, offering higher strength and more precise part designs. The main advantages of this technology include:
- Enhanced Strength and Rigidity: The combination of SMC and PHC materials provides higher strength while reducing waste during production.
- Fine Processing: The one-piece molding technology allows for the production of more complex part shapes, meeting the high design requirements of automotive and industrial products.
- Cost Reduction: By using this integrated molding process, material waste is minimized, improving production efficiency and reducing costs.
Conclusion
As the demand for high-performance, low-cost components continues to grow, PHC material molding and SMC-PHC one-piece molding technology are becoming increasingly popular in various industries. Whether in the automotive industry, aerospace, electronics, or construction, PHC materials demonstrate exceptional performance, making them a key material in modern manufacturing. As technology continues to advance, PHC composites will play an even more vital role in many fields.